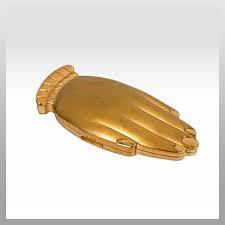
Satin Gold Plating
Satin Gold Plating is another form of very rich classic electroplating techniques. It displays rich and characteristic features of real gold of the ancient times.
Practically, we will generally deposit a thin layer of pure gold over a layer of satin nickel when producing a satin gold finish. We will then protect the finish with e-coat to give the performance that is necessary. This is generally more economical than trying to obtain the desired performance results with a thicker layer of pure gold to achieve a wide range of finishes. The photo displayed above is our standard color but we can match a wide variety of colors.
Prior to being electroplated the item, which is to be satin gold plated, must first go through a mechanical staining operation. This is where the texture and gloss of the finish are developed depending on the media used while staining. Once the item has been satined it then enters the electroplating operation. The photograph above displays an item which has been satined, gold plated and protected with e-coat.